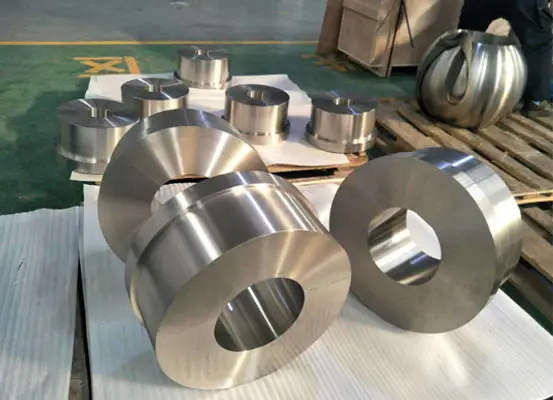
A titanium billet is subjected to external forces during the forging process in order to generate plastic deformation, modify size, shape, and performance for the production of mechanical components, workpieces etc. In addition, depending on the slider movement, there are horizontal and vertical slider motions.The automation level is further influenced by the forging forces necessary, the process, and the material utilization rate etc.
Titanium forging materials are mainly pure titanium and titanium alloy.The material may be purchased in its pure form as bars, ingots, metal powder, and liquid metal. The forging ratio is the ratio of the metal’s cross-sectional area before deformation to its cross-sectional area after deformation. The proper selection of forging ratio, reasonable heating temperature and holding time, reasonable starting forging temperature and final forging temperature, reasonable deformation and deformation speed, and reasonable forging temperature and speed all work well together to improve product quality and lower costs.Typically, billets for small and medium-sized forgings are round or square bars. The bar has consistent and good mechanical qualities, precise shape and size, good surface quality, and is simple to arrange for mass production. It also has good grain organization. Excellent performance forgings may be forged out of them without a significant forging deformation as long as the heating temperature and deformation circumstances are controlled reasonably.
- Forging can be classified as open die forging, extrusion, die forging, no-flash die forging etc. according on how the billet is moved. Because the no-flash die forging has no flashes , the material utilization rate is higher,so it is possible to complete the finishing of complex forgings with one or several processes. The forging area is smaller and the required load is likewise smaller since there are no flashes. However, it is important to take precautions to ensure that the billet is not entirely constrained. For this reason, the volume of the billet should be strictly regulated, the relative position of the forging die should be controlled.The forgings should be measured, and efforts should be made to lessen the forging die’s wear.
- Forging can be classified as swing rolling, roll forging, ring rolling etc. according on how the forging die moves.Roll forging can be used as a pre-process for thin materials to increase material utilization. Similar to open die forging, rotary forging is partial forming and has the benefit of requiring less forging force than open die forging relative to the size of the forged item. It is challenging to achieve precision in this kind of forging, especially open die forging, since during processing the material extends from the vicinity of the die face to the free surface.
Care should be taken to avoid overloading at the lower dead point and to regulate speed and die position if great precision is desired. This is because they will affect the die life, forging tolerances, and form correctness. Additionally, consideration should be given to actions such modifying the slide guide clearance, guaranteeing stiffness, regulating the lower dead point, and employing subsidised drives in order to maintain precision.