Laser welding is a new type of welding, laser welding is mainly for thin-wall materials, precision parts welding, spot welding, butt welding, overlap welding, sealing welding, etc., Its features include a small weld width, a high depth to width ratio, a small heat affected zone, little deformation, and quick welding speed. After welding, there is no need for handling—the weld is flawless and requires only a quick processing step. The weld has high quality, no porosity, can reduce and optimize the impurities of the base material, the tissue can be refined after welding, and the strength and toughness of the weld are at least equal to or even more than the base metal. Precise control, small focus point, high precision positioning, easy to achieve automation. It can realize the welding between some dissimilar materials.
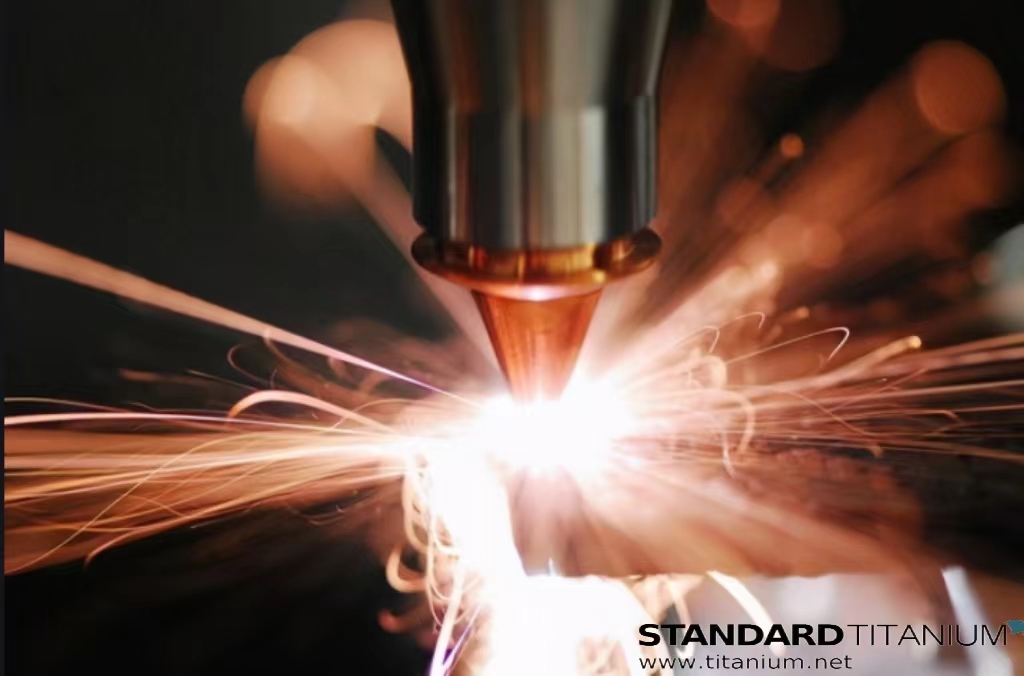
1. Laser self - fluxing welding
Using a laser beam with good work-related properties, such as high power density and directivity, is necessary for laser welding. The laser beam is concentrated in a tiny area and welded rapidly using an optical system to create a highly concentrated heat source region that melts solder and forms solid solder joins and welds. A large depth to width ratio, excellent speed and precision, minimal heat input, and minimal distortion are some advantages of laser welding. invasive-free welding Not requiring a vacuum, it is insensitive to magnetic fields.
2. Laser welding with filling wire
The process of pre-filling a particular welding material in the weld and melting it with laser irradiation, or filling the welding material simultaneously with laser irradiation, to form a welding joint, is known as laser wire filling welding. Laser wire filling welding addresses the issue of stringent requirements for work piece preparation and assembly when compared to non-wire welding. Thicker pieces can be welded with smaller power; the micro-structural characteristics of the welded area can be regulated by changing the filler wire’s composition.
3. Laser scanner welding
One type of laser welding technique is remote laser welding, which processes great working distances using a high-speed scanning lens. high efficiency, rapid welding speed, low welding duration, and high positioning precision; it won’t obstruct the welding fixture and won’t pollute optical lenses; Welds of any shape can be tailored to maximize structural strength, among other benefits. In most cases, there is more splash and no gas protection for the weld. It is extensively utilized in body covering portions made of galvanized and thin, high-strength steel plates.
4. Laser brazing
The laser beam emitted by the laser generator is focused on the surface of the welding wire and heated, so that the welding wire is heated and melted (the base material is not melted) to wet the base material, fill the joint gap, and combine with the base material to form a weld to achieve a good connection.
5. Laser swing welding
By swinging the reflection lens inside the welding head, the laser swinging is controlled to stir the welding solution pool to promote the gas overflow from the solution pool and refine the grain. Simultaneously, it is possible to lessen the sensitivity of laser welding to incoming material gaps. Particularly well suited for welding copper, aluminium alloy, and other incompatible materials.
6. Laser-tig arc hybrid welding
In order to create a new and effective heat source, laser-tig arc hybrid welding combines two types of laser and arc heat sources with various physical characteristics and energy transmission techniques. Features of composite welding: 1. Bridge ability is improved compared to laser welding, which benefits the organization. 2. little deformation, fast welding speed, and deep penetration in contrast to arc welding.