Titanium Alloy in Aerospace
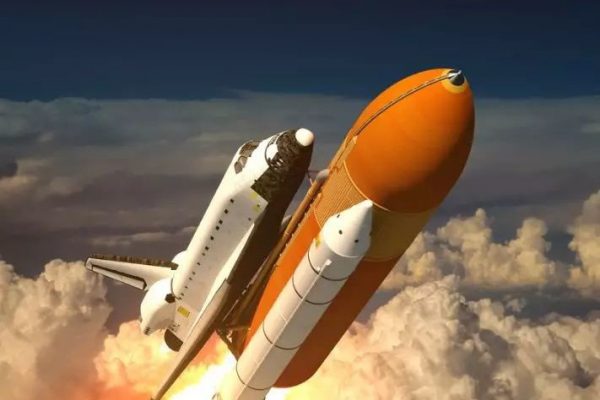
As we all know, titanium has a low density. However, titanium alloys are exceedingly strong and ductile. It can operate effectively at 500°C and -220°C. Because of these benefits, titanium alloy has become the primary choice of spaceship material.As early as the second half of the last century, superplastic forming technology was successfully applied to the production of titanium alloy. The technology solved a number of problems in the production and processing of titanium alloy.It has been constantly upgraded and optimized, and able to fully utilize the characteristics of titanium alloy. The weight of the component was decreased by 35%, while the production cost was lowered by approximately 60%.
In general, titanium alloy has been widely employed in spacecraft. Its utilization is also the only path forward for future space development. However, due to technological and economic restraints, titanium alloy use has not completely realized its promise or opened up the market. Spacecraft will need to employ better performance titanium alloys in the future, as well as continuing to lower prices and enhance the efficiency of titanium manufacturing.
Types of Titanium Alloy in Aerospace
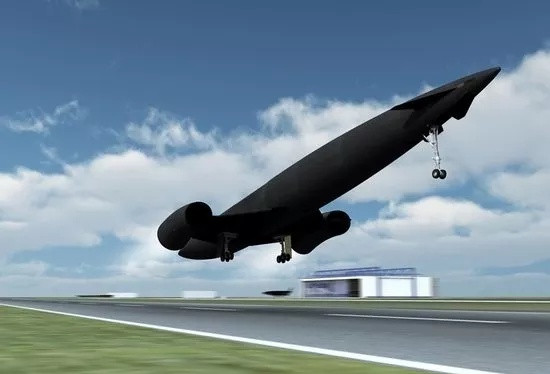
- Ductile titanium alloy
Currently, only titanium alloy 47121 is utilized for satellite launch, which is insufficient to satisfy The Times’ requirements. The primary titanium alloys, such as Ti-2Al-1.5Mn, have low strength and toughness. Under 1200mpa, they are significantly lower than the spacecraft requirements for titanium alloy toughness. Therefore, it is vital to continue research and develop titanium alloys with high toughness and high strength, as well as increase and diversify their applications in the aerospace industry. - High temperature titanium alloy
Since titanium alloys must operate well at high temperatures in the operational environment of spacecraft, this area of study is extremely important. However, it can be challenging and even counterproductive to guarantee this. The first high temperature titanium alloy, known as titanium alloy 6Al4V, was created in the United States in 1956. It can be used at about 300°C and has found excellent applications in the space shuttle and intercontinental missile.Nevertheless, due to the technology’s limitations at the time, titanium alloy 6Al4V has a number of drawbacks, including being challenging to produce and difficult to process. The temperature was raised to 450°C during the subsequent improvement procedure by adding some zinc, manganese, silicon, and other components. - Low temperature titanium alloy
With the continuing expansion of space exploration distance, titanium alloy is increasingly being utilized in low temperature environments. And the lower the temperature, the higher the strength of titanium alloy. Thus, the study in this field is crucial. Experiments reveal that intermediate elements such as H and O may be sieved out of titanium alloy, hence improving its performance at low temperatures.Titanium alloy LT600 developed in Japan can adapt to a temperature of 25K. Its flexibility and fracture toughness are well matched, and has been utilized to build liquid hydrogen pumps. The titanium alloy A7ELI developed in China offers stronger strength, improved plasticity, and meets the thickness criteria of space vehicles. - Casting titanium alloy
Casting titanium alloy has exceptional corrosion resistance and is simple to weld. However, in the process of casting, titanium’s melting point is higher. Meanwhile, its chemical properties are unusually lively. During welding, titanium reacts easily with air and other materials, resulting in embrittlement. Therefore, these reasons restrict the development of titanium alloy casting technology. After long-term experiments and research, it was discovered that titanium alloy 5Al can accommodate manufacturing needs. - Powder titanium alloy
Although the benefits of titanium alloy are clear, owing to the high price, the application must be evaluated in many aspects and cannot be supplied on a wide scale. Many nations have spent a long time researching how to minimize the production cost of titanium alloy. They eventually develop powder metallurgy technology and realize commercial use. In the United States, for example, there are already a number of companies with the technology to produce powder titanium alloy, and achieve large-scale production.
Conclusion
Titanium alloy has been widely employed in spacecraft as a new metal material due to its performance benefits. With the fast advancement of science and technology, it is critical to fully utilize sophisticated technology in titanium alloy research and development, as well as continual exploration, innovation, and enhancement of titanium alloy production technology.
Standard Titanium has 29 years of production expertise in the titanium industry and produces not only basic titanium products, but also aerospace and military titanium,which are more challenging materials. Additionally, we hold ISO 9001 and AS 9100D certifications. We are convinced that you will be satisfied with our reasonable pricing, superior quality, and excellent after-sales support.