Introduction
Metallic materials have long been introduced into people’s life. Modern biomedical functional materials started from 1930s. At first, stainless steel has been developed for implant and medical applications. Second material is cobalt-based alloy. At around 1960s Titanium and its alloy followed the pace becoming the newest generation of metallic biomaterials. Since its first appearance, titanium has been described as a miracle metal and has received extensive attentions.
What makes titanium so special?
As a transition metal, titanium is characterized as low density, and high strength. It is resistant to corrosion under various conditions. Most importantly, titanium is inert and immune to body fluid and tissue. These are the so-called biocompatibility and corrosion resistance. They are key requirements for medical applications.
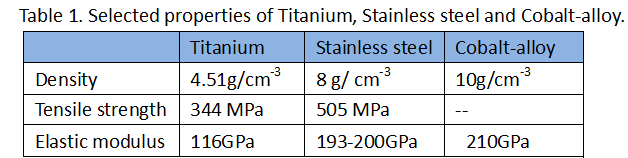
Table 1 describes basic properties of Titanium, stainless steel and cobalt-alloy. Titanium has lowest density of 4.51g/cm-3, while Stainless steel has density of 8 g/ cm-3. With comparable tensile strength, titanium ends up with much higher strength to density ratio of 76 kN·m/kg. It is 20% higher than stainless steel (strength/density 63 kN·m/kg). The elastic modulus value of titanium is only half of conventional stainless steel and cobalt-alloy. It is much closer to human bone. Also titanium is non-ferromagnetic and has low thermal expansion and conductivity.
Titanium and its alloy have most useful properties make them huge success in orthopedics, implants, and surgical instrument fields. Standard Titanium Co. is a manufacturer and supplier of titanium and Cu-Ni metal mill and finished products covering the widest range of mill products, grades and dimensions.
Situated at the centre of titanium production in China, Standard Titanium Co. brings the lowest pricing and highest engineering standards for metals to the market. Confident that we cannot be beaten on prices and quality we have introduced our price promise guarantee. Customers worldwide choose Standard Titanium as their trusted and reliable supplier of titanium and CuNi mill and finished products.
Artificial joint and Medical implant
World population is getting older. We now live in a very active life and desire to be living longer. Injuries caused by hard sports, road traffic and other accidents are everywhere. Obviously, the demand of artificial joint continues to grow. Titanium and its alloys have been commonly used to fabricate implant devices such as: artificial hip joints, artificial knee joints, bone plates, screws for fracture fixation, cardiac valve prostheses, pacemakers and artificial hearts. Each year more than 100 million patients in the world received replacement therapy and more than 1,000 tones of titanium being implanted into patients’ body worldwide.
Mechanically, these metal implants must be formed to certain shape and maintain functions during the usage period. Our daily activities include bending, twisting, squeezing and muscle contraction. These artificial parts must not be deteriorated when subjected to fatigue, abrasion and impact loads. Titanium has 50% less weight and 20% higher strength/density ratio of stainless steel. It is lighter and stronger. When implant inside human body, it will reduce body loads. Patients will feel more flexible and active. There will be stress between artificial part and human body. The so-called interface stress is caused by mismatch of elastic modulus. From table 1, we can see that titanium has lowest elastic modulus among these three materials. The mechanical compatibility of titanium implant and human bone is much better.
Physiologically, the body rejects foreign parts. When use stainless steel and co-alloy as biomaterials, clinical inflammation, redness, and itching often occur after implant operation. Titanium and titanium alloys are well known as biologically inert metal materials. In the immersion environment of human blood they have excellent corrosion resistance. It resists human blood and cell tissue very well, ensuring good compatibility. There is almost no pollution and allergic reactions, which greatly improves the patients’ recovery. This is the basis for the widespread applications of titanium.
In general, commercially pure titanium (Cp Ti) is considered as the best candidate because pure titanium has best biocompatibility. But Ti-6Al-7Nb, Ti-13Nb-13Zr, Ti-12Mo-6Zr and Ti-6Al-4V ELI alloy are also widely used in medical implants. Check our website to inquire about our diverse products!
Orthopedic equipment
The main task of orthopedics is to adjust bone deformities. The twisted body needs external force to help it return to normal position. Orthopedics equipment should provide strong supporting and remember the correct shape of the body. Besides wear resistance and corrosion resistance, the unique property required here is shape memory. Titanium-nickel shape memory alloys have both strong strength and memory properties. At present, common bone plates, intramedullary nails, mandibular internal fixation, scoliosis correction and so on are made with Ti-Ni alloy.
Dentistry Implants
Dental implant is a bit different. There are three types of dental implant: osseointegrated, mini-implant for orthodontic anchorage, and zygomatic. Titanium has been used as crowns, crown nails, fixed bridges, porcelain bridges, adhesive bridges, denture retaining rings, bases, connecting devices and strengthening devices. Almost all metal parts of dentures have been covered by titanium.
Let us start from typical osseointegration. First, doctor will put a ‘root’ or “seed” into the jaw bone. After it settles down, the superstructure of the tooth will bond with the implant. Then new tooth will grow on top of it. Here is the difference between medical implant and dental implant. Medical implant is a replacement of failed hard tissue or a “glue” or “screw” to connect broken hard tissue. But dental implant helped new structure to grow. How fascinating!
This “simple” procedure requires excellent biocompatibility and thermal property. When drinking soup and eat ice cream people will feel hot and cold, but these feelings are from the mouth not the teeth. Healthy teeth won’t get any stimulation.
Titanium has very low thermal expansion. When titanium-based implant used as a “root”, it won’t expand or shrink inside people’s mouth. The newly formed tooth will stay where it should be. Titanium has very low thermal conductivity, only 1/5 of stainless steel, 1/3 of aluminum and 1/2 of copper. When used as crown, it won’t transfer to real teeth structure. Titanium can protect the dental pulp from heat and cold stimulations.
In dental field, precision casting titanium has the characteristics of high dimensional accuracy, no bubbles and shrinkage. Currently, 4 commercially pure titanium (Cp Ti) are specially used for dental implant applications. They are ASTM grades 1 to 4. They all have low level of electronic conductivity, high corrosion resistance, thermodynamic state at physiological pH values, low ion-formation tendency in aqueous environments and isoelectric point of the oxide of 5-6.
From grade 1 to 4, purity decrease and strength increase. Grade 2 titanium is the most popular star for dental implant applications. It has minimum yield strength of 275 MPa which is comparable to annealed austenitic stainless steels. When require higher strength, titanium alloy can also be applied. Ti-6Al-4V and other alloy are also used in various situations.
Surgical instruments
In the development of surgical instruments, first-generation is carbon steel, after electroplating treatment their performance could not meet the requirements of clinical use. Often cause infection. Second generation is austenitic stainless steel, but the chromium composition is toxic and has certain impact on the human body.
In the manufacture of surgical instruments, mechanical properties and ductility are the first issues that need to be considered. The metal must have a certain ductility to maintain required shape without defects. Some basic surgical instruments are long and thin, such as scalpels, tweezers and scissors. To ensure the safety of operation, the instrument needs a certain degree of strength. They need to be tough enough and not to break during surgery. The minimum modulus required for surgical instruments is 100 GPa. Titanium has modulus of 116 GPa.
During surgery operation, instruments directly exposed to living tissue. Corrosion resistance, biocompatibility and magnetic properties are required. Titanium is non-toxic to human tissue. It won’t cause any immune response. Operating room sometimes is under magnetic fields. For example, MRI generates a magnetic field of about 1.5 Tesla. This magnetic field can affect surgical instruments in a variety of ways, including: harmful motion caused by magnetic field interaction (namely missile effect), instrument heats up due to radio frequency (RF) power deposition and photography related to instrument use. Titanium is non-magnetic, guaranteed safety of operation. It’s non-magnetic also eliminate the threat of damage to tiny and sensitive implanted electronic devices.
After surgery, sterilization process is carried under hot steam spray at high temperature. Various detergents are used to clean bacteria and infections. After repeated clean, instrument should not change size and the surface quality should not be affected. Wear and tear should also be minimal. Surgeons need instruments that work properly every time they use it. Titanium and titanium alloys have good corrosion resistance. The work temperature can range from 150 oC to 500 oC.
Last but not the least, light weight of titanium makes it particularly suitable for microsurgery. Lightweight surgical instruments can reduce surgeons’ fatigue, especially during long-term operations.
In the field of medical equipment, medical titanium and titanium alloys are high-quality metal materials and are widely used. Laser electrodes, dental drills and forceps are often made from titanium.
Summary
As a leading manufacturer and supplier company, Standard Titanium Co. offers customized solutions for a wide range of applications. At every stage of the manufacturing process, we work closely with you to ensure that the final product meets your need. To find out more, feel free to contact us or request a quote today.