Applications
Medical Field
Titanium is known as a “biological” metal, with non-toxic, harmless, high temperature resistance, high corrosion resistance, high strength, low density, good biocompatibility, and other advantages.Moreover, elastic modulus is close to that of human tissue, occupying around fifty percent of the medical metal field. Currently, orthopaedics and dentistry use titanium alloys most frequently for 3D printing.
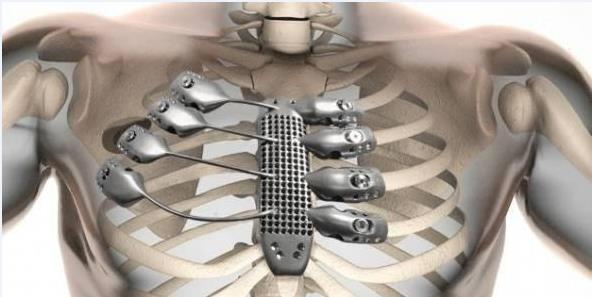
Mold Field
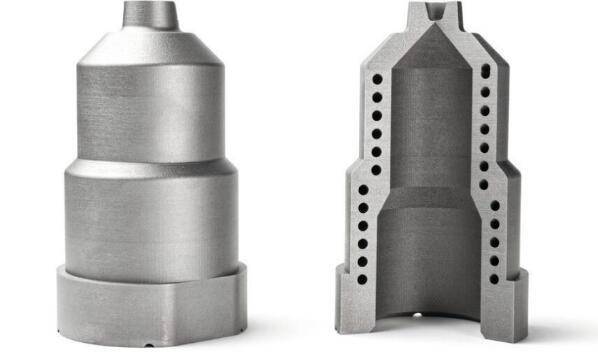
Aerospace Field
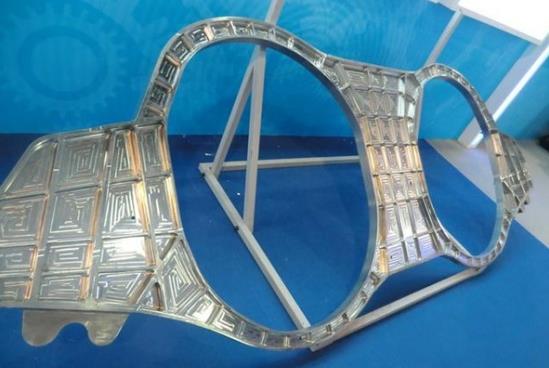
Advantages
- The 3D printing technique can generate a range of complex-shaped components, cut manufacturing time, and lower production costs.
In aircraft applications, the use of titanium 3D-printed components can save purchase costs. A term derived from the aerospace industry refers to the correlation between the weight of the purchased material and the weight of the final product.
In conventional production, the buy-to-sell ratio for titanium airplane parts, for instance, can range between 12:1 and 25:1. Therefore, 1 kilogram of parts requires 12 to 25 kg of raw materials.
Metal 3D printing might cut the titanium ratio from 12:1 to 3:1. This is because metal 3D printers typically use only the amount of material necessary to create a product, and the supporting framework generates minimal waste. Cost savings for pricey materials, such as titanium, are less relevant than reduced procurement costs.
- Titanium’s lightweight qualities can be enhanced by topology optimization in additive manufacturing.
Engineers utilize topology optimization software to establish requirements such as load and stiffness limitations.Then, software tools optimize the initial design to fulfill these requirements.
With this optimization, all extraneous materials may be eliminated from the design, resulting in a lightweight and resilient component. Typically, topological optimization designs can only be created via additive manufacturing methods.
This advantage is particularly beneficial to the aerospace industry, as lightweight 3D-printed titanium components may reduce aircraft weight and enhance aircraft performance.
- Additionally, 3D printing can be utilized to directly create and repair items. Aerospace components are expensive and have a sophisticated construction. When errors or flaws arise, losses can reach hundreds of thousands or even millions of dollars. 3D printing saves time and money by using the same material to correct the problem and build a full shape.
Challenges
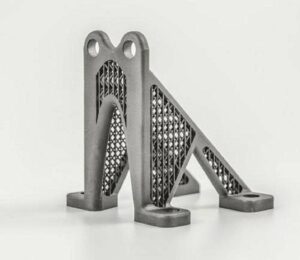
While 3D printing with titanium offers various benefits, it also presents some challenges.
- The necessity of defining standards for the additive manufacturing of titanium. There are already businesses working in this route.
- The expense of titanium powder is the second difficulty.
Titanium powder suitable for 3D printing, for instance, costs between $300 and $600. In the aerospace, medical, and automotive industries, 3D titanium printing has shown to be a vital technology. Titanium’s exceptional characteristics, paired with 3D printing’s capacity to eliminate waste and produce intricate, lightweight designs, are the key reasons.