Different Cutting Methods for Titanium
Titanium plate cutting by shearing machine is easy to deform and difficult to straighten.Grinding wheel blade cutting, on the other hand, is usually utilized for titanium bar and pipe. Shearing, laser, plasma, and water jet cutting are the most common methods for cutting titanium plates.
Most laser cutting equipment cannot cut metal plates thicker than 12mm due to the limits of present laser technology. Furthermore, laser cutting equipment is costly. Laser cutting technology is also limited as a result of this. Manufacturers should first consider employing a shearing machine for titanium plates with a thickness of less than 12mm. Plasma cutting is used by most Chinese producers for titanium plates thicker than 12mm.
Plasma cutting is a type of melting cutting. The heat-affected zone of titanium absorbs enormous amounts of hydrogen and carbonization during the cutting process, causing the material’s physical and chemical properties to deteriorate. Water jet cutting is a cold processing method, meaning the workpiece is cut at a lower temperature. There is no heat-affected zone or thermal deformation, and so on. As a result, it has advanced quickly in the titanium cutting process.
About Water Jet Cutting
Working Principle
Ordinary water is pressurized to 400 MPa or higher for water jet cutting. It ejects water through a small nozzle at a speed of about three times the speed of sound (1000m/s). High-speed dense water jets are used to cut the material.
Technical Features
- Extensive cutting range.
It can cut non-metallic as well as hard, brittle, tough materials such as titanium alloy, porcelain, glass, composite materials, and so on.
- High cutting precision.
There is no heat-affected zone or delamination phenomenon on the cut surface. As a result, post-sequence polishing is rarely required following water jet cutting, lowering processing costs. The method enhances the material utilization ratio since the kerf is so tiny.
- High Productivity .
Multiple nozzles can be configured on the water jet cutting system. The workpiece is cut to the exact size required. It will reduce the number of intermediate processes and boost production.
- Excellent adaptability.
Cutting can begin at any point on the workpiece and in any direction. It can handle pieces that are tough to process using traditional methods. It’s simple to combine with CNC technology to produce small batches of complex shaped parts.
- Safe and clean.
There is no dust, no odor, no toxicity, no sparks, low vibration, and low noise during cutting. Hence, it is particularly well suited to hard and dangerous working environments requiring explosion-proofing.
Water Jet Cutting VS Plasma Cutting
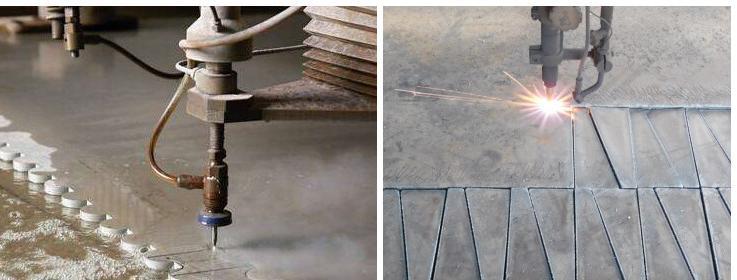
- Cutting precision and speed
To cut GR.2 20mm thickness titanium plate, use water jet cutting technology (WP402 water jet cutting machine) and plasma cutting technology (CNCTMC precision plasma cutting machine). The data demonstrates that, while water jet cutting speed is slower than plasma cutting, water cutting accuracy is higher than plasma cutting. It will help to improve the quality of later processing.
- Before and after cutting, the chemical compositionof titanium changes
Samples were taken 3mm from the edge of GR.2 titanium materials cut with water jet and plasma technology, and chemical compositions were determined. The chemical composition of titanium changes little after water jet cutting, but its physical and chemical properties remain mostly constant. The chemical composition of titanium material changes dramatically following plasma cutting, as do the physical and chemical properties.
- Titanium’s processability before and after cutting.
The processability of titanium material after water jet cutting is the same as it was before.Titanium is difficult to secondary process after plasma cutting because the cutting surface contains high hardness hydrogen, oxides, and carbides.