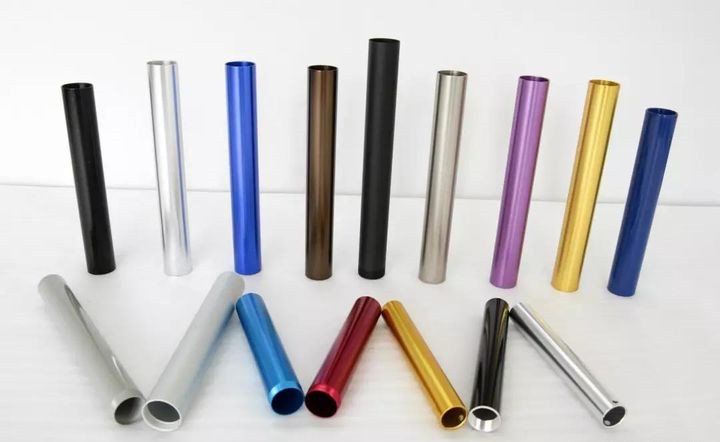
Anodizing is a conventional method of electrolytically oxidizing the surface of metals and their alloys to generate an oxide coating. This method produces oxide films with uniform color, corrosion resistance, high adhesion, and biocompatibility. It is commonly utilized in contemporary biomedicine and aerospace industry.
Titanium is anodized using titanium as the anode and other metals such as stainless steel as the cathode. The surface of the titanium alloy is oxidized by an electrochemical process with the assistance of a specific electrolyte to generate an oxide coating. This layer of oxide film has extremely visible light reflection and refraction effects. The oxide film with varied thicknesses will exhibit different colors while also providing protection.Therefore, it is an ideal ornamental and wear-resistant layer that is frequently employed in structures, aviation, medicine, and other disciplines.
The anodizing coloring process
Degreasing (strong alkaline degreaser) → Water washing → Initial pickling (hydrofluoric acid aqueous solution) → Water washing → Secondary pickling (hydrofluoric acid + hydrogen peroxide aqueous solution) → Water washing → anodizing (Constant voltage electrolysis in phosphoric acid solution) → Water washing → Sealing → Drying.
1. Degreasing
Degreasing is used to remove any oil residue left on the titanium surface after rolling. Due to the low water permeability of the oil-attached component, pickling the titanium surface might result in uneven coloration.
2.Initially pickling
Titanium and its alloys’ surfaces are pear-shaped after the first pickling process. The titanic acid wash containing 5% by weight of hydrofluoric acid can stimulate the creation of pear skin pattern.
3. Secondary pickling
The purpose of the second pickling is to eliminate the powdery dirt created by the initial pickling. In order to prevent uneven pickling, it is also important to utilize an aqueous solution of hydrofluoric acid and hydrogen peroxide to stabilize the titanium ion into a titanium-containing complex after the surface dirt has been dissolved by hydrofluoric acid.
4. Anodizing
For constant voltage treatment, the aluminum plate was utilized as the cathode and the prepared titanium plate as the anode, with phosphoric acid as the electrolyte at 1% weight concentration. As the voltage increases, the oxide deposit on the titanium surface thickens and changes color.
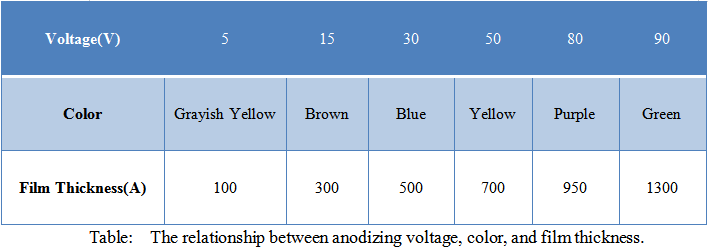
5. Sealing
In order to increase corrosion resistance, pollution resistance, and wear resistance of the anodized coating,titanium and its alloys must be sealed with hot water, steam, and solutions containing inorganic salts and organics after anodizing and coloring .
6. Drying
After sealing, use a clean cotton towel to remove any moisture from the workpiece and allow it to dry naturally.
To summarize, the anodizing process of titanium and its alloys is very simple. The color created on the surface is rich, and the cost is relatively low. Therefore, it is easily popularized in the industry and has a strong development promise technology for oxidative coloration.