With the rapid development of the automobile industry in recent years, global automobile production and ownership have increased day by day. While cars make travel more convenient, they also cause three major problems: fuel consumption, environmental protection, and safety. In terms of sustainable development, it is particularly urgent to reduce fuel consumption and pollution emissions. According to statistics from international authoritative departments, the weight of the automobile consumes approximately 60% of the fuel used by automobiles. For every 10% reduction in a car’s weight, exhaust emissions and fuel consumption can be reduced by 10% and 7%, respectively. As can be seen, weight reduction and light weighting of automobiles are effective measures for achieving the aforementioned goals.
There are two main ways to achieve lightweight automobiles: optimizing the automobile frame structure and using lightweight materials in automobile manufacturing. Aluminum, magnesium, titanium alloys, and other metals are the most common light alloys used in automobiles currently.
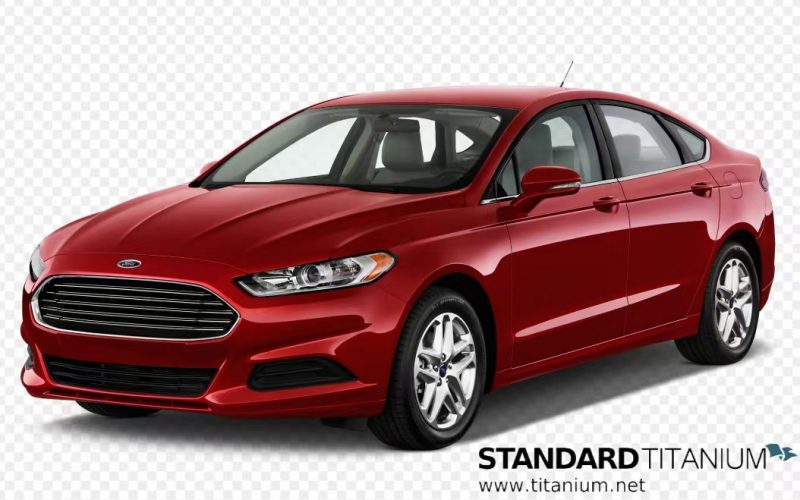
Application and Characteristics of Titanium Alloys in Automobiles
Titanium alloy is a novel structural and functional material with excellent overall properties, a low density, and a high specific strength. It has a density of 4.51g/cm3, which is between aluminum (2.7g/cm3) and iron (7.6g/cm3). The specific strength of titanium alloy is higher than aluminum alloy and steel, and the toughness is close to steel. Titanium alloy has superior corrosion resistance to stainless steel, particularly in marine atmospheric environments, chloride ions are eroded and in micro-oxidizing atmospheres. It also retains good plasticity, and the working temperature of heat-resistant titanium alloy can reach around 550°C, making it significantly more heat resistant than aluminum alloy and magnesium alloy. It also has good processability and welding performance.
Since the industrial production of titanium, the excellent properties of titanium and titanium alloys have attracted the attention of various cutting-edge industries . With the start of the titanium industry, titanium materials entered the automobile industry in the mid-1950s. Enter the 1990s, with the global energy shortage and people’s increased awareness of environmental protection, particularly in the automobile industry, the United States, Japan, and Europe promulgated a series of ecological laws and regulations on fuel efficiency, CO2 emissions, vehicle weight reduction, and so on. Automobile safety and dependability demand higher standards.
Titanium parts used in automobiles
Titanium can be used to make valves, valve springs, valve spring bearing seats, and connecting rods in the engine system, and the chassis parts are mainly include springs, exhaust systems, axle shafts, and fastener. In addition, suspension springs, piston pins, turbocharger rotors, fasteners, lug nuts, bumper brackets, door beams, brake caliper pistons, pins, clutch discs, pressure plate, shift button are also included.
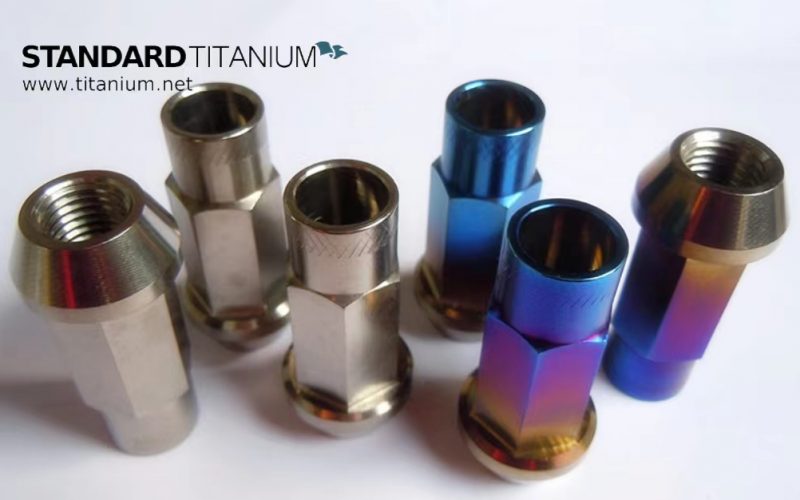
Another factor of the high cost of titanium alloys is the high cost of alloying elements. With the advancement of titanium smelting technology, adding leftovers, scraps, and other residues produced during production as furnace charges after a series of treatments to realize cycle production, it is an efficient way to lower raw material costs.
Titanium metal has a high melting point, very active chemical properties, and has a strong chemical affinity for elements such as O, H, N, and C, which makes pure titanium extraction difficult. The Kroll magnesium reduction method widely used in producing sponge titanium. It has a high energy consumption, a long cycle, and cannot be produced continuously. meanwhile, a large amount of metal magnesium is used as a reducing agent, which has a relatively high production cost.