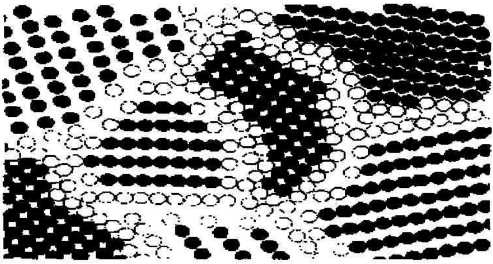
1. Surface mechanical grinding technology
Surface mechanical grinding is the earliest method applied to nanometer material surface. The projectile in a closed container is driven by a vibrator to vibrate at high speed. And it makes the projectile hit the top sample at different angles. As the number of impacts increases, the material’s surface plastic deformation gradually refines the grain.
2. Surface mechanical milling technology
Surface mechanical milling is a new type of metal surface self-nano technology. The cylindrical sample rotates relative to the hemispherical WC/Co tool at the speed of v1. The tool moves along the axial direction of the processed sample at the speed of v2. Under the influence of a predetermined pressure, the tool tip makes contact with the sample’s surface. Therefore, the friction of the contact surface results in a plastic deformation area.
3. High energy shot peening technology
Shot peening technology is widely used in industrial production. It mainly launches a large number of high-speed projectiles to impact the surface of the material. Therefore, it causes plastic deformation and changes the surface stress to improve the surface performance of the material.
4. Ultrasonic impact technology
Ultrasonic waves are used to transfer ultrasonic impact technology to the impact terminal via the intermediate mechanism. A high impact load will break the surface grain of the material and produce high density dislocation. In this manner, the material’s surface has been nanometerized.
5. Supersonic fine particles bombarding (SFPB)
The gas-solid two-phase flow(GSF) idea is used in Supersonic Fine Particles Bombarding. The supersonic airflow drives a large number of hard particles to bombard the surface of the material. With high kinetic energy and frequent bombardment, the material surface experiences severe plastic deformation , Meanwhile, it refines the grain to the nanoscale.
6. Laser shock processing
Laser shock processing irradiates the material’s surface with high-power laser pulses, and the plasma explosion caused by the thermal vaporization of the absorbing layer on the material’s surface will generate high-pressure shock waves, which will act on the surface of the material and generate residual stress.
7. Outlook
- The surface nanolayer formed by surface self-nanocrystallization is relatively thin, with a thickness of several hundred microns, however, it is not significant enough to improve the overall performance of the material. As a result, we can investigate the full influence of deep surface nanostructure layer on the performance of titanium alloy.
- Other surface strengthening technologies such as surface coating and surface deposition can be merged with self-nano process, to develop hybrid nano technology, improve treatment efficiency and optimize material properties.
- Titanium alloy is commonly used in aircraft engines. It is very important to study its fatigue, wear and corrosion behavior under complex working conditions such as high temperature, high pressure and vibration, so it is necessary to conduct more in-depth research on surface nanoization
At present, there are few researches on the simulation of titanium alloy surface self-nanoization, so it can be integrated with mechanics, materiology, and other fields. Establishing the corresponding relationship between relevant process parameters and nanostructure gradients through simulation models, so as to guide the development of engineering practice