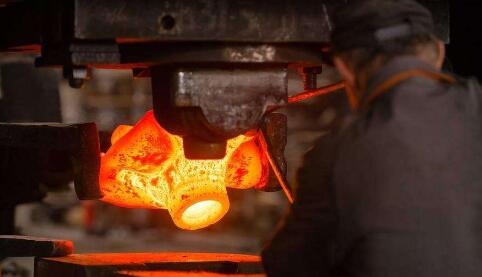
Titanium and titanium alloys are widely used in various fields due to their advantages of low density, high specific strength and good corrosion resistance. In order to make better use of these materials, researchers have done a lot of research on their forging process.
Forging is a plastic forming method that utilizes the malleability of metal.It creates the blank material under the impact or pressure of tools in order to get a certain shape and structure qualities. Forging manufacturing can not only achieve the shape of mechanical components, but also enhance the internal structure of materials and the mechanical qualities of components.
1. Hammer Forging
In general, hammer forging is accomplished between two flat moulds or section moulds without moulding chamber. The tool utilized in hammer forging has simple shap, high flexibility, short manufacturing cycle and low cost. Nonetheless, the labor intensity is high, the operation is tough, the productivity is low. And the forging quality is inadequate. The processing allowance is substantial. Therefore, it is only applicable in a few instances where the product’s performance has no specific criteria.
2. Open-die Forging
The blank deforms between two chambers in the modules. The forgings are restricted inside the chambers. Excess metal flows out of a narrow slit between the two molds, forming burrs around the forgings. The metal is forced into the shape of the chamber by the resistance of the die and the surrounding burrs.
3. Closed-die Forging
During closed die forging, no transverse burrs are formed perpendicular to the direction of die motion. The chamber of closed die has two functions: shaping and guiding the blank.
4. No-draft Forging
There are two types of no-draft forging: extrusion die forging and reverse extrusion die forging. No-draft forging can produce all kinds of hollow and solid pieces with great accuracy size and denser interior structures.
5. Multi-ram Die Forging
In addition to the vertical punching plunger, there are two horizontal plungers. The ejector is used for punching. The ejector pressure is higher than that of a typical hydraulic press ejector. During multi-ram die forging, the slider operates alternately and jointly from both vertical and horizontal directions on the workpiece.One or more punch holes are employed to cause the metal to flow outward from the center of the die cavity in order to fill the die chamber. There are no specific forging burrs on the barrel components’ parting line.
6. Partial Die Forging
Sectional die forging, pad forging, and other partial die forging techniques can be utilized to forge large integral forgings under the current hydraulic pressure. Because the forgings are processed one segment at a time using the partial die forging technique, the equipment tonnage needed can be small. In general, this technique may be applied to medium-sized hydraulic presses to treat large forgings.
7. Isothermal Die Forging
Prior to forging, the die is heated to the forging temperature of the blank. The die and blank are maintained at the same temperature throughout the die forging process. Therefore, substantial deformation may be produced with tiny deformation forces. Isothermal die forging is comparable to isothermal superplastic die forging, with the exception that the blank is superplastically treated prior to die forging in order to generate equiaxed grains.
Titanium alloy forging is widely used in the aviation and aerospace manufacturing industries.It is also becoming increasingly popular in the automotive, electric power, and shipbuilding industries.
Standard Titanium has 29 years of production expertise in the titanium industry and produces not only basic titanium products, but also aerospace and military titanium, which are more challenging materials. Additionally, we hold ISO 9001 and AS 9100D certifications. We are convinced that you will be satisfied with our reasonable pricing, superior quality, and excellent after-sales support.