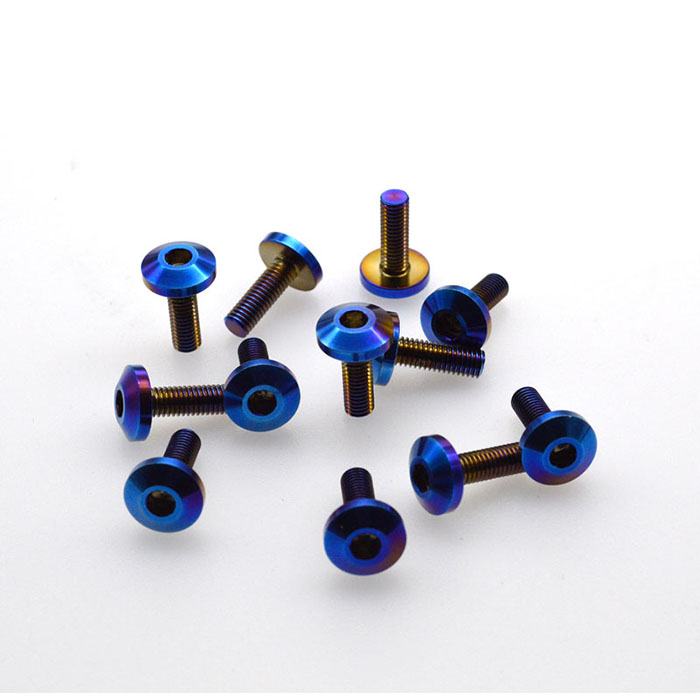
Analysis of Titanium Alloy Processing
- Low thermal conductivity. At 200°C, l=16.8W/(m.K) for GR.5, which is just 1/4 of steel, 1/33 of aluminum, and 1/25 of copper. Poor heat dissipation and cooling during the cutting process are resulting in tool wear.
Low modulus of elasticity. Parts have been machined surface rebound, resulting in machined surface and tool contact area rises, affecting not only the dimensional accuracy of the parts but also the tool’s longevity.
Hardness factor. High hardness value titanium alloy processing is simple to make the tool generate chipping and abrasion. Low hardness value titanium alloy processing will be sticky, chip in the cutting edge of the front surface of the tool near the development of chip tumor, affecting the processing effect. Due to these properties, titanium alloy parts only remove 1/4 as much metal during machining as equivalent-sized steel ones do.
Strong chemical affinity. Titanium can not only chemically react with the main components of air, nitrogen, oxygen, and carbon monoxide, to form TiC and TiN hardened layers on the surface of the alloy.However, it can also react with the tool material under the high temperature conditions generated by the cutting process, reducing the tool’s durability.
Insufficient cutting safety. Titanium is a combustible metal, and the high temperatures and sparks generated during the micro cutting process may cause titanium chips to ignite.
Titanium Alloy Processing Method
-
Use carbide-tipped tool as much as possible. Titanium alloys can be processed with them since they are resistant to chemical reactions at high temperatures and have high strength and superior thermal conductivity than tungsten cobalt alloys.
-
Reasonable selection of tool geometry parameter . To reduce cutting temperature and tool bonding, the front angle of the tool can be appropriately reduced to dissipate heat by increasing the contact area between the chip and the front tool surface. At the same time, the back angle of the tool is increased to reduce tool bonding and machined surface accuracy due to frictional contact between the machined surface rebound and the back tool surface. And the tool tip should adopt a circular to ensure a sharp edge shape and smooth chip removal. Titanium alloy should be resharpened on a regular basis.
-
The ideal cutting conditions. Refer to the following program to determine the cutting parameters: Lower the cutting speed since a high cutting speed will cause the cutting temperature to rise quickly; Moderate feed – feed tiny cutting edge owing to cutting in the hardened layer of time and wear accelerated; Feed big cutting temperature is high; Longer tool life can be achieved by cutting deeper layers of titanium alloy with the tool’s tip.
-
To lower the cutting temperature, the machining region should be completely and constantly cooled while the cutting fluid flow and pressure should be high.
-
When choosing machine tools, it’s important to strengthen stability to reduce vibrational tendencies. Blade chipping and other types of blade damage can happen from vibration. Additionally, titanium alloy processing rebound, significant clamping force will enhance the deformation of the workpiece, so finishing can be taken into consideration when utilizing the assembly fixture and other auxiliary support to fulfill the process system rigidity requirements.
-
Climb milling often uses the milling technique. Conventional milling of titanium alloys results in far more serious milling tool damage than climb milling because of chip sticking and chipping milling cutters.
-
Grinding wheel clogging because of sticky chips and surface burns on the parts is a regular issue. Because of this, green silicon carbide grinding wheels with sharp abrasive grains, high hardness, and good thermal conductivity should be used.The grinding wheel grit should be between F36 and F80 depending on the surface finish.The grinding wheel hardness should be soft to reduce the adhesion of abrasive grains and chips and reduce the grinding heat.The grinding feed should be small, the speed should be low, and the emulsion should be adequate.
-
Standard drill bits must be resharpened while drilling titanium alloy to prevent tool burning and drill bit breakage. Repair techniques include raising the top angle, lowering the cutting part’s front angle, raising the cutting part’s back angle, and double the number of cylindrical edge taper. The number of retreats should be increased. The drill shouldn’t stay in the hole. The chips should be removed in time. The emulsion should be sufficiently cooled. The drill should be observed to become blunt, and the drill should be replaced and resharpened in time.
-
The typical reamer must also be adjusted for titanium alloy reaming. The edge band’s width must be smaller than 0.15mm, and the cutting and calibration parts must be rounded to prevent a sharp point. The spindle speed should be a little slower while reaming the hole with the group reamer, which can be used numerous times with each reaming increasing the reamer diameter by no more than 0.1mm. With this technique, reaming, a high degree of finish standards can be satisfied.
-
The hardest component of manufacturing titanium alloy is tapping. The tap teeth will quickly wear out from too much torque, and the tap may even break in the hole due to the processed part’s rebound. To increase the chip space, the number of teeth should be decreased in proportion to the diameter. The back angle should be raised to about 30° after leaving a 0.15mm-wide edge on the calibrated teeth. Between half and a third of the teeth’s back should be removed. And the calibrated teeth should be kept for three buckles to increase the number of taper. It is advised that leaping taps be used to reduce the area of contact between the tool and the workpiece.
Processing Notes
The tool is meticulously resharpened and sharpened to produce as little cutting heat as possible during the machining process.
- All equipment, tools and fixtures should be kept neat and clean, and chips should be removed as soon as possible.
When transferring titanium chips, use non-combustible or non-flammable tools. Dispose of chips in non-combustible containers that are well covered.
When operating cleaned titanium parts, clean gloves should be worn to avoid stress corrosion caused by sodium chloride later.
Cutting area with fire suppression equipment.
Micro cutting, cutting off the titanium chips once the fire is extinguished with a dry powder fire extinguishing agent or dry soil, dry sand.
Conclusion
Titanium machining is more difficult than most other metal materials, as well as more constrained. However, titanium alloys can also produce satisfactory results if the proper tools are employed and the machine tool and configuration are tailored to their machining needs.