All-titanium vessel uses the titanium material for all major components, including the shell, head, and nozzle. Minor parts may be made of materials other than titanium. Carbon steel can be used, for instance, to make the lopper flanges and the joint bolts.
The thickness of the all-titanium vessel shell must be at least 2 mm in order to assure geometric tolerance, meet thickness requirements for welding, and meet stiffness requirements for manufacture, transportation, and lifting. And it saves titanium materials and reduces costs.
Design Principles
All-titanium vessel structures are not appropriate for high temperature, high or medium pressure, and big equipment applications because the mechanical strength of titanium material reduces greatly and the elastic modulus is low when the temperature is more than or equivalent to 200°C.
The maximum temperature for an all-titanium pressure vessel is 250°C, and it is thought that all-titanium construction is more cost-effective for small and medium-sized vessels with a pressure of 0.5 MPa and a temperature below 150°C. It might not be cost-effective to use pure titanium when the thickness is larger than 13mm.
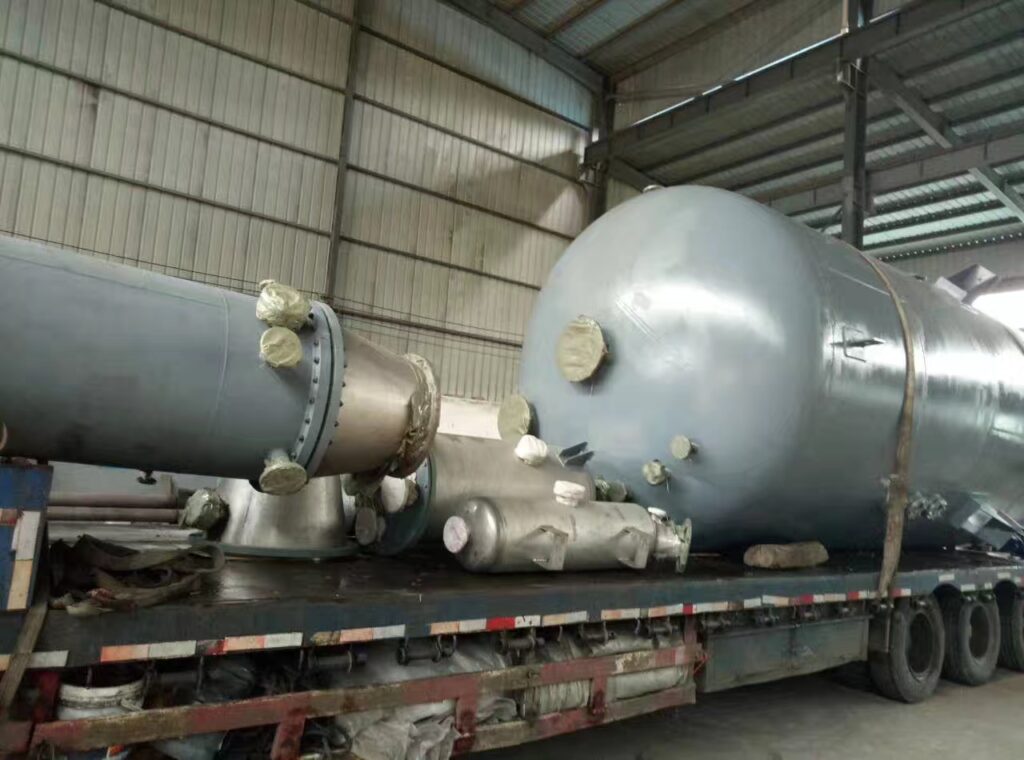
Structure Requirements
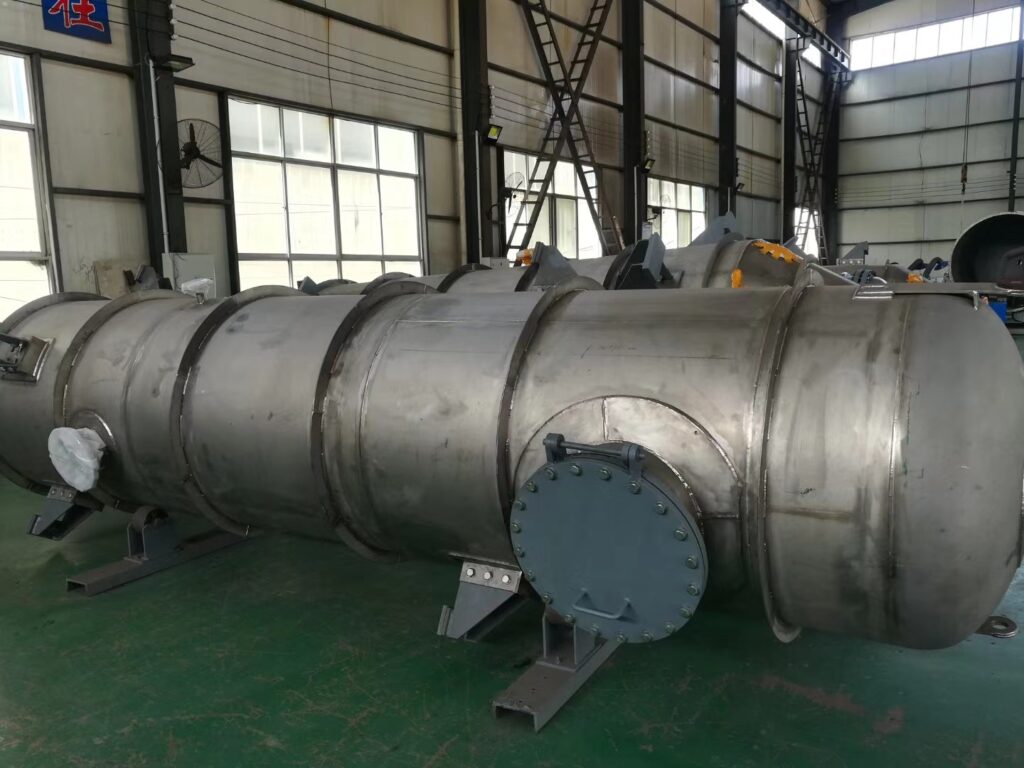
- When designing a welding structure, the welding components must be easy to use with hydrogen arc welding equipment. And any high temperature (over 400°C) welding joint regions must be well protected. In molten state, titanium can combine with almost any element, so special protection must be taken during welding and hot working. As much as possible, the nozzle opening on the shell should be perpendicular to the shell’s axis in order to ensure adequate protection. This makes the protective fixture more convenient and improves the effectiveness of the protection.
- Strictly prevent interfusing steel and titanium while welding. Only explosive welding and brazing can join titanium and steel together since other metals like iron will combine with titanium during the welding process to generate hard and brittle intermediate metal compounds, drastically reducing the ductility of the weld.
- The butt welding joint’s blunt edge clearance should be adequate. Due to titanium’s high melting point, weak thermal conductivity, low heat capacity, high resistivity coefficient, and high fluidity in the weld pool, the blunt edge clearance of the butt welded joint of the all-titanium pressure vessel is less than that of steel.
- To prevent stress concentration as much as possible, the design of titanium vessels should guarantee the continuity of the structure and the smooth transition of welded joints.
- The bending radius and flanging of titanium parts should be larger (than those of steel), and the expansion rate of the tubes should be lower.
- In some media, industrial pure titanium is prone to crevice corrosion. Crevices and stagnant zones should be avoided as much as possible when designing and handling vessels in contact with these media. In the crevices, titanium alloys (such as titanium and palladium alloys) or coatings are used.
- Measures should be taken in the structure (such as the use of a third material as a transition layer) or anode protection in the design and treatment of vessels in contact with electrically conductive corrosive media if it is found that contact between titanium and other metals can lead to galvanic corrosion.
- When designing equipment that is prone to corrosion, the critical velocity of the corrosive medium should be kept below it, and it is best to avoid sudden changes in flow direction or velocity. Alternatively, protective baffles can be installed in parts that are prone to corrosion and abrasion.