Pressure Shell
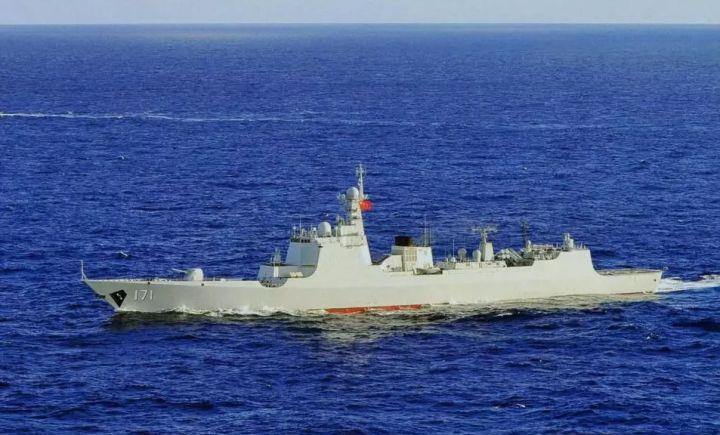
Deep diving vehicles and submarines are the primary applications of titanium alloy pressure shells in the ship industry. Titanium alloy has high specific strength, superior corrosion resistance, and non-magnetic qualities, making it an excellent material for producing pressure-resistant shells for deep-sea equipment.
Russia is the first nation to adopt titanium alloy pressure shells on nuclear submarines and the global leader in technology. Since the 1960s, Russia (the former Soviet Union) has produced a series of submarines made of titanium alloy. Initially, the No. 661 cruise missile nuclear submarine was constructed. Later, 7 “Alpha”-class submarines made of titanium alloy, 1 “Mike”-class submarine, and 4 “Sierra”-class submarines were produced in succession. These nuclear submarines are all attack kinds, with the “Alpha”-class submarines employing up to 3,000t of titanium alloys. The “Typhoon” class nuclear submarine, manufactured in Russia, is the world’s largest submarine in terms of volume and tonnage. Its titanium content exceeds 9,000t. Currently, Russia’s newest generation of “North Wind” class nuclear submarines also features pressure-resistant titanium alloy hulls.
Power Propulsion
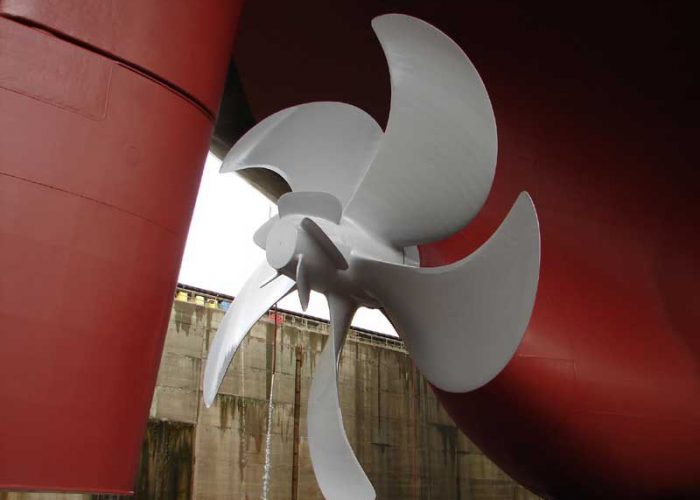
Due to the effects of seawater and maritime climate, ship propeller materials must possess strong corrosion fatigue strength and cavitation resistance. Titanium alloy is superior to copper alloy and steel in these aspects. In addition, because of the low density in comparison to other regularly used materials, propellers made from titanium alloys have a smaller mass than that made from other materials. Therefore, ships with propellers made of titanium alloy are more efficient.
In the 1960s, Russia, the United Kingdom, and others began experimenting with titanium alloy propellers for ships. In its “Alpha” and “Mike” class nuclear submarines, Russia has utilized titanium alloy propellers, for instance. On numerous ships, the United States has also utilized titanium alloy propellers.
Acoustic Device
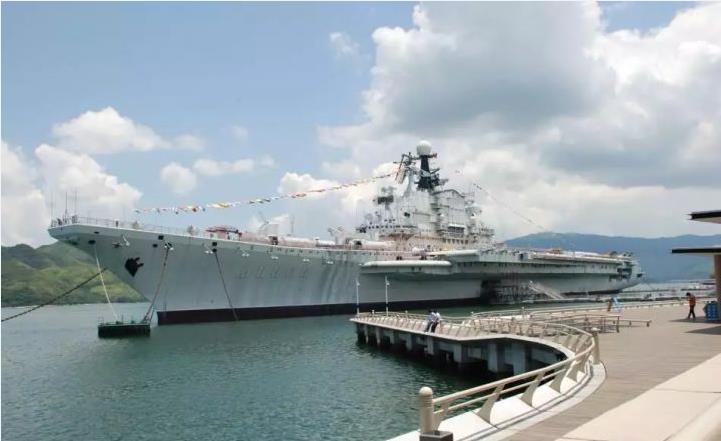