As an essential structural alloy, titanium alloy continues to benefit mankind in various fields.
So far, the worldwide titanium alloy yearly output has exceeded 40,000 tons.The globe is continually exploring new uses for titanium alloy, with a strong commitment to entering the civil industry with a vast market potential.
Titanium Alloy"Three Brothers"
Titanium alloy has three types of matrix structure (various titanium alloy structure).Titanium alloy is divided into three categories: α alloy, (α+β) alloy and β alloy.
- α titanium alloy
Single-phase alloys (composed of one kind of alloy) have a stable microstructure and exceptional oxidation resistance at both normal and elevated temperatures. At 500°C to 600°C, it retains its strength and creep resistance.
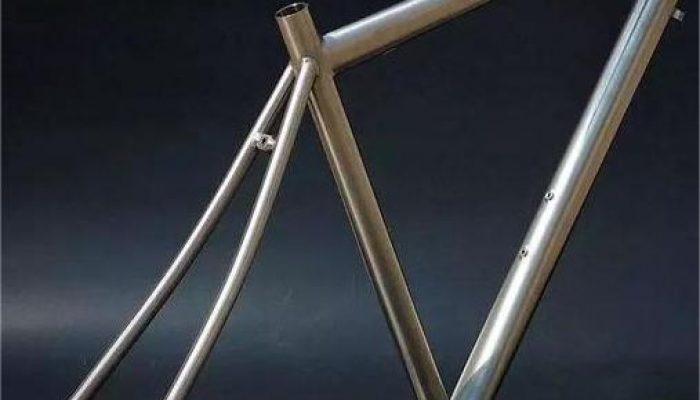
- β titanium alloy
Single-phase alloys have strong strength. After quenching and aging, the alloy is further strengthened.However,its thermal stability is low, making it unsuitable for high-temperature application.
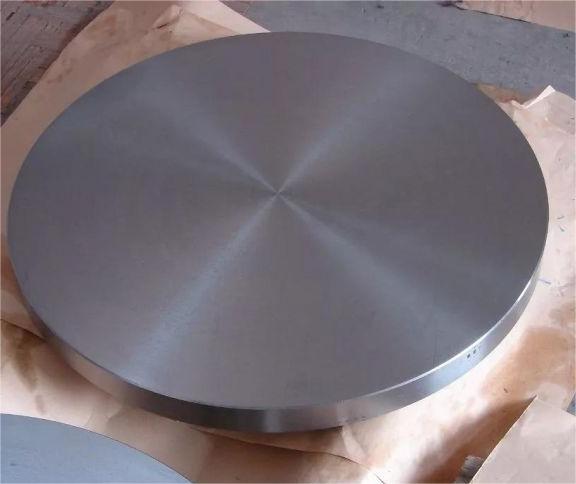
- α+β titanium alloy
Duplex alloy (made of two different types of alloys) has strong comprehensive characteristics. Besides, it has excellent microstructure stability, toughness, plasticity, and high temperature deformation performance. It may be strengthened by hot pressure processing. Quenching and aging also make it strengthened.Compared to α titanium alloy, its thermal stability is lower .
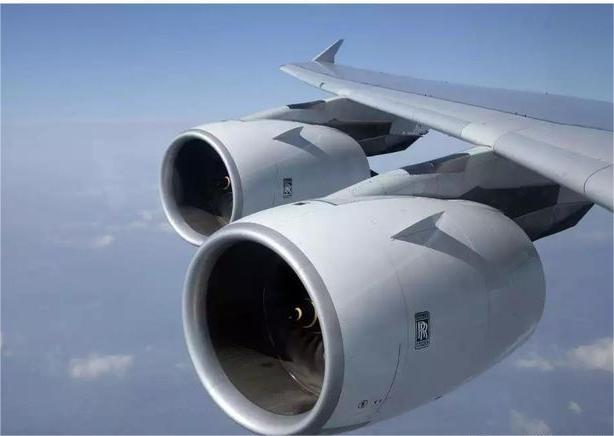
Titanium Alloy Processing Technology
- Vacuum smelting technology
Use a vacuum smelting furnace to smelt alloy. The titanium alloy is melted into liquid by the eddy current generated in the furnace. The benefit is that the entire process is carried out in a vacuum, preventing contaminants in the air from entering the metal and smelting high grade alloy.
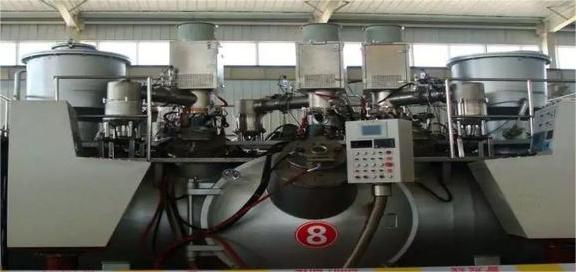
- Isothermal forging technology
Isothermal forging is achieved by heating the die to the billet deformation temperature and deforming at a low strain rate.
Titanium alloy isothermal forging technology is a new process.It combines with thermo-mechanical treatment to obtain the optimal comprehensive mechanical properties of titanium alloy isothermal forging. However, the cost of die materials, manufacturing, and heating device are higher than the cost of conventional forging.Therefore, the technology is mostly used to manufacture aircraft parts.
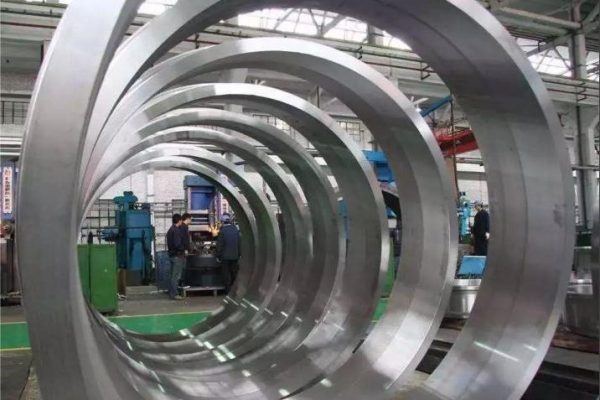
- Cold forming
Without any heating, the titanium alloy may be processed using cold forming techniques like as punching, shearing, bending, and stretching.
The unique processing methods for titanium alloys include laser processing, electron beam processing, ion beam and plasma processing, electric processing, and others. These methods are used to mill titanium alloys based on economic considerations.
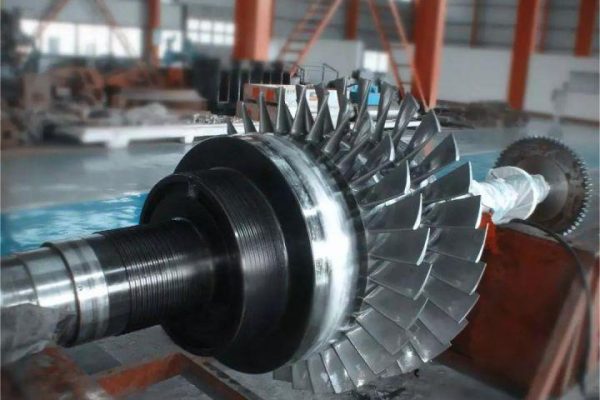
- Surface treatment
the method of creating a surface layer on top of a titanium alloy substrate that differs from the substrate in terms of mechanical, physical, and chemical characteristics.
According to the properties of titanium alloy, plasma infiltration, ion, electron, and laser beams are currently used along with other standard modern surface treatment techniques.It primarily increase titanium alloy’s wear resistance, corrosion resistance, fretting wear resistance, and high temperature oxidation resistance.
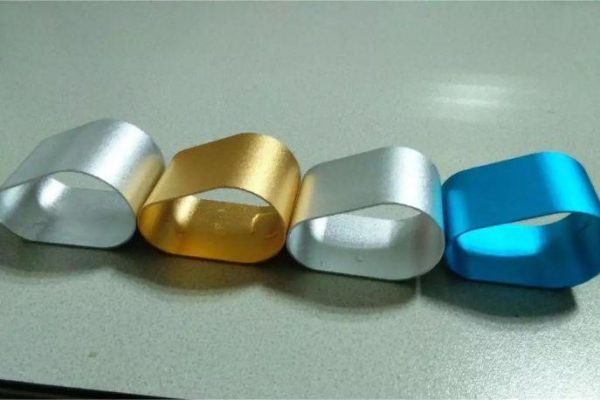
Currently, the “three brothers” of titanium and titanium alloy are evolving in various integrated application technological directions.Many scientists around the world are actively researching how to use more affordable, superior technology to increase production and benefit mankind.
Situated at the centre of titanium production in China, Standard Titanium Co. brings the lowest pricing and highest engineering standards for metals to the market. Confident that we cannot be beaten on prices and quality we have introduced our price promise guarantee. Customers worldwide choose Standard Titanium as their trusted and reliable supplier of titanium and CuNi mill and finished products.