Tin foil, copper foil, aluminium foil, and other metal thin sheets are examples of foils. Foil refers to any metal sheet with a thickness of 0.2mm or less. Heavy gauge foil, medium gauge foil, and light gauge foil are categorised according to the thickness of the metal foil. The thickness ranges from 0.2mm to 0.1mm for heavy gauge foil, 0.1mm to 0.09mm for medium gauge foil, and 0.001mm for light gauge foil.
At the moment, the thinnest foil that can be rolled in an industrial setting is 0.0045mm thick. Aluminium foil currently produces the most, accounting for over 85 percent of worldwide metal foil production. China is the leading producer and exporter of aluminium foil in the world. In 2021, the output was 4050 KT, or around 65 percent of the global total.
Titanium foils are difficult to produce, expensive and low yielding. Therefore, titanium foils are not widely used. Aircraft skin insulation material is one of its high-end applications.As we know, when an aircraft is in the air, its outer metal skin will heat up due to intense friction with the air. In order to prevent heat from entering the interior, an aircraft must have the heat insulation protective layer (Figure 1).
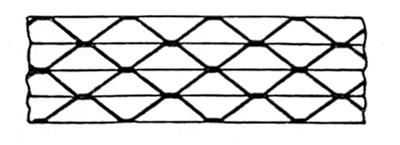
It is welded by four layers of heat insulation plates, with a thinner flat layer in the middle. Figure 2 shows a diagram of the heat insulation plate part, made from 0.08mm TB2 alloy foil. TB2 is β titanium alloy.
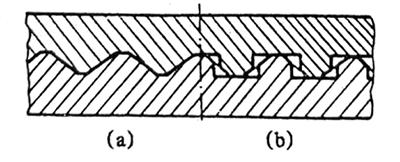

In the countries such as the United States and France, manufacturers use superplastic forming technology to produce titanium foil insulated plates . Although the technology can process high quality heat insulation plates, the production cycle is long. And the workpieces are in high temperature state for a long time, they will absorb oxygen. Titanium no longer has oxidation resistance above 649 ℃. Hence, it will absorb more oxygen and become brittle, so that the mechanical properties will decline. In addition, superplastic forming is suitable for simple workpiece shape.For the complex workpiece shown in Figure 2, it is difficult to superplastic forming, because moulds processing is not easy.
As the heat insulation plate is diffusion welded, the oxygen content should be precisely and strictly controlled. Therefore, it is best to weld in a vacuum furnace. However, it requires expensive equipment, which increases the investment and makes the operation more difficult. For this reason, a research institute in China has proposed sheath protection technology and successfully manufactured titanium foil aircraft heat insulation plate with low cost and high quality.
Notes of Sheath Technology:
- Clean the surface of titanium plate material and sheath carefully. The surface cannot have oil stains and impurities.
- Select sheath material carefully. The sheath cannot leak under high temperature and emit any gases. Besides, materials with low strength at high temperature should be choosen to reduce deformation resistance, improve moulds life and ensure the dimensional accuracy of the workpiece.
- Sheath should be coated with a thin and uniform layer of solder resist, so as to avoid sheath is welded with the titanium foil. However, the solder resist cannot emit any harmful gases at high temperatures and should not contain water, glue or other substances.